1. Røde ovnsten falder ned
Årsag:
(1) Når roterovnens overflade ikke er ordentligt ophængt.
(2) Cylinderen er overophedet og deformeret, og den indre væg er ujævn.
(3) Ovnforingen er ikke af høj kvalitet eller udskiftes ikke til tiden efter at være blevet slidt tyndt.
(4) Roterovnens cylinders centerlinje er ikke lige; hjulremmen og klodsen er stærkt slidt, og cylinderens radiale deformation øges, når mellemrummet er for stort.
Fejlfindingsmetode:
(1) Blandnings- og kalcineringsoperationen kan styrkes.
(2) Kontrollér nøje afstanden mellem hjulremmen og klodsen nær brændzonen. Når afstanden er for stor, skal klodsen udskiftes i tide eller justeres med klodser. For at forhindre og reducere slid forårsaget af langvarig bevægelse mellem klodserne, bør der tilsættes smøremiddel mellem hjulremmen og klodsen.
(3) Sørg for, at ovnen er stoppet under drift, og reparer eller udskift roterovnens cylinder, hvis den deformeres for meget, med tiden;
(4) Kalibrer regelmæssigt cylinderens centerlinje og juster støttehjulets position;
(5) Vælg ovnforinger af høj kvalitet, forbedr indlægskvaliteten, kontroller nøje brugscyklussen for ovnforinger, kontroller murstenstykkelsen i tide, og udskift slidte ovnforinger i tide.
2. Støttehjulets aksel er knækket
Årsager:
(1) Tilpasningen mellem støttehjulet og akslen er urimelig. Prespasningen mellem støttehjulet og akslen er generelt 0,6 til 1/1000 af akseldiameteren for at sikre, at støttehjulet og akslen ikke løsner sig. Denne prespasning vil dog få akslen til at krympe for enden af støttehjulshullet, hvilket resulterer i spændingskoncentration. Det er ikke svært at forestille sig, at akslen vil knække her, og det er tilfældet.
(2) Udmattelsesbrud. På grund af støttehjulets komplekse kraft, hvis støttehjulet og akslen betragtes som en helhed, er akslens bøjnings- og forskydningsspænding størst ved den tilsvarende del af enden af støttehjulets hul. Denne del er tilbøjelig til udmattelse under påvirkning af skiftende belastninger, så bruddet bør også forekomme ved enden af samlingen mellem støttehjulet og akslen.
(3) Produktionsfejl Rulleakslen skal generelt smedes, bearbejdes og varmebehandles med stålbarrer eller rundstål. Når der opstår defekter i midten, som ikke opdages, såsom urenheder i stålbarren, insekthud fra smedede insekter osv., og der opstår mikrorevner under varmebehandlingen. Disse defekter begrænser ikke kun akslens bæreevne, men forårsager også spændingskoncentrationer. Som kilde til dette er brud uundgåeligt, når revnen udvider sig.
(4) Temperaturbelastning eller upassende kraft. Opvarmning af de store fliser i roterovnen er en almindelig fejl. Hvis drift og vedligeholdelse er forkert, er det let at forårsage overfladerevner på rulleakslen. Når de store fliser opvarmes, skal akslens temperatur være meget høj. Hvis akslen på dette tidspunkt afkøles hurtigt, kan den hurtigt krympende akseloverflade på grund af den langsomme interne afkøling af akslen kun frigive den store krympespænding gennem revner. På dette tidspunkt vil overfladerevnerne producere spændingskoncentration. Under påvirkning af alternerende belastning vil revnen, når den udvider sig i omkredsen og når en vis grad, knække. Det samme gælder for overdreven kraft på rullen. For eksempel forårsager forkert justering for stor kraft på akslen eller en bestemt del af akslen, hvilket let kan forårsage brud på rulleakslen.
Udelukkelsesmetode:
(1) Forskellige interferensmængder anvendes i støttehjulets og akslens indeslutningsområde. Da interferensmængden mellem støttehjulet og akslen er stor, vil akslen krympe på dette sted, efter at enden af det indre hul i støttehjulet er varmmonteret, afkølet og strammet, og spændingskoncentrationen er for stor. Derfor reduceres interferensmængden af de to ender af det indre hul i støttehjulet (område på ca. 100 mm) gradvist indefra og ud under design-, fremstillings- og installationsprocessen for at mindske forekomsten af halsdannelse. Reduktionsmængden kan gradvist reduceres til en tredjedel til halvdelen af den midterste interferensmængde for at undgå eller reducere halsdannelsesfænomenet.
(2) Omfattende fejldetektion for at eliminere defekter. Defekter vil reducere akslens bæreevne og forårsage spændingskoncentration, hvilket ofte forårsager brudulykker. Skaden er stor og skal tages alvorligt. For støttehjulets aksel skal defekter findes på forhånd. For eksempel skal materialevalget inspiceres før bearbejdning, og der må ikke vælges problematiske materialer; fejldetektion skal også udføres under bearbejdningen for at eliminere defekter, sikre akslens indre kvalitet og samtidig sikre akslens bearbejdningsnøjagtighed og eliminere revnekilder og spændingskoncentrationskilder.
(3) Rimelig justering af ovnen for at reducere yderligere belastninger. Flere rulleaksler bærer hele ovnens vægt gennem rullerne. Belastningen er meget stor. Hvis installationen eller vedligeholdelsesjusteringen er forkert, vil der opstå excentrisk belastning. Når afstanden fra ovnens centerlinje er inkonsekvent, vil en bestemt rulle blive udsat for for stor kraft; når rullens akse ikke er parallel med ovnens centerlinje, vil kraften på den ene side af akslen øges. Forkert overdreven kraft vil forårsage, at det store leje opvarmes og vil også forårsage skade på akslen på grund af den store belastning på et bestemt punkt på akslen. Derfor skal vedligeholdelse og justering af ovnen tages alvorligt for at undgå eller reducere yderligere belastninger og få ovnen til at køre let. Undgå at starte ild og svejse på akslen under vedligeholdelsesprocessen, og undgå at slibe akslen med en slibeskive for at reducere skader på akslen.
(4) Undgå at afkøle den varme aksel for hurtigt under drift. Under ovnens drift vil det store leje forårsage opvarmning af forskellige årsager. For at reducere produktionstab anvender nogle enheder ofte hurtig afkøling, hvilket let kan forårsage mikrorevner på akseloverfladen, så langsom afkøling bør anvendes for at undgå hurtig afkøling.
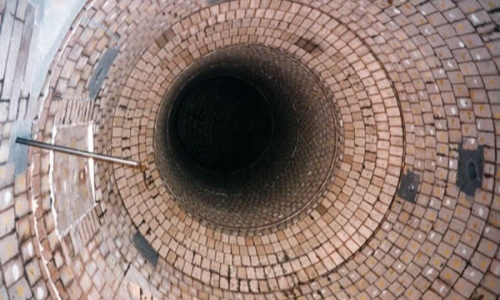
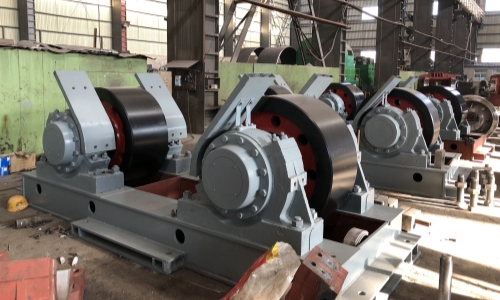
Udsendelsestidspunkt: 12. maj 2025